Our PP/PET extrusion line is designed to produce strapping band with a wide range from 4 up to 32 mm. The line is controlled and monitored through PLC. It can switch between PET or PP straps without any downtime.The Gneuss MRS extruder eliminates the work intensive drying and crystallisation processing of the PET flakes. This results in a significant reduction of footprint and energy requirement.Using this process, a raw material (such as plastic) is melted and pushed through a die with one or more openings to form the desired shape. During this extrusion, the polymer chains are aligned by stretching, which increases the tensile strength of the strap.Plastic straps are used to secure and reinforce parcel shipments. They are a preferred packaging solution over glue systems, plastic self-adhesive tapes, and staples. They are especially effective for sealing regular slotted cartons (where box flaps align) and telescoping cartons.
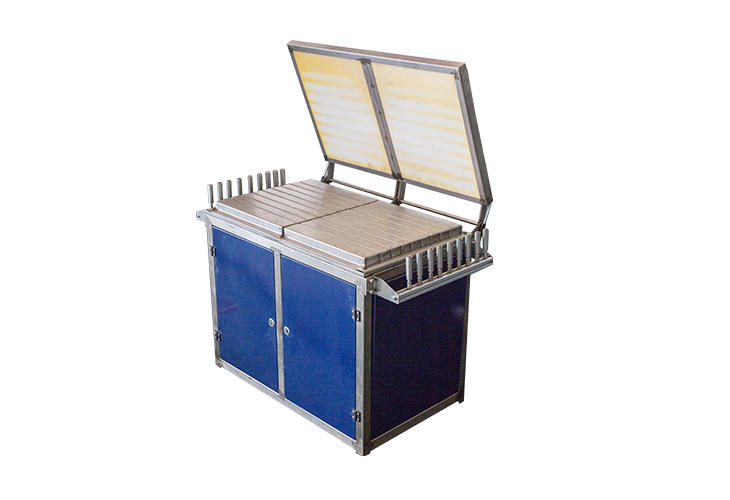
Straps can be made from either multi-strand or sheet extruded plastic. Both processes start with a wide extrusion that is then slit and oriented in both length and width directions. Orientation makes it possible to increase the tensile strength of the resulting strap by up to 10 times over an unorientated strand. An orientated strand also resists crack initiation and propagation in the welded strap sections. This feature makes oriented straps particularly suitable for use in a friction weld system, which uses hot blade fusing to fuse the strap together.The present invention relates to a method for producing oriented PET strap. The oriented material is made by using a co-extrusion process whereby a high strength layer and an outer oriented layer are extruded together. The high strength layer is preferably a high strength polyethylene terephthalate and the outer layer is a low melting point material.
Straps produced by the method of the present invention have a significantly higher corner strength than conventional PET strap. In addition, the oriented PET strap has improved stress relaxation properties, which is important in applications requiring long hauls and rough handling.It eliminates time and energy intensive drying and crystallisation, while achieving high melt purity and high tensile strength. The line is fully automated and controlled by PLC to ensure maximum production performance and product quality.Printed plastic strapping adds a professional finish to your packaging. It also improves visibility, allowing you to identify your shipment more easily. This can help reduce mishandling and damage. Additionally, it helps keep items secure and increases the overall safety of your goods.
Using the energy-saving VACUREMA technology, residual moisture and other chemical contaminants are already removed before extrusion. This ensures high quality PET strapping with excellent elongation and strength characteristics.This line is capable of producing a range of widths, including 9.5-19mm. It features a hydraulic control system, embossing design, synchronization control system, precise adjustment on the position of embossing roll and embossing strength. In addition, this line is able to use 100% bottles of recycled materials, reducing cost for users. This machine is suitable for small-scale production of PP and PET packing belts. It is easy to operate and has a high profit margin.The machine produces high-quality PET straps with embossing and printing machines, which can be used to secure cartons, wooden boxes, bricks and other goods. This equipment is designed and manufactured by using optimum grade raw material and advanced technology in synchronization with set industry standards.